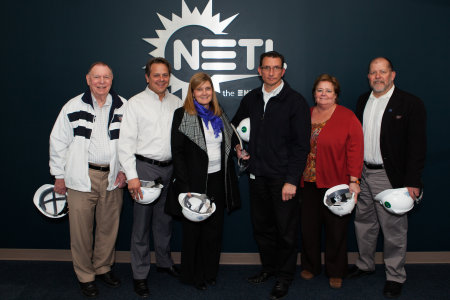
On January 1, 2016 EIO submitted the Final Technical Report for a $500,000 Advanced Manufacturing project sponsored by the U.S. Department of Energy's National Energy Technology Laboratory. Working with industry, EIO tailored two material processing technologies, Hot Isostatic Pressing of Powdered Metal, (HIP/PM) and Additive Manufacturing (AM), (also known as 3D Printing) to create a credible, safe and cost effective approach to large scale manufacture of quality structural advanced material components. For expensive high nickel alloy components, EIO's R&D activities have shown numerous advantages of using HIP/PM over other methods such as casting and forging.
A serious drawback of HIP/PM has been the canisters required to produce the parts. The cans (or outside skins of the powder metallurgy container) are currently formed by bending and welding low carbon steel sheet metal, constraining the complexity and shape. Under this program, EIO successfully demonstrated that 3D Printing could be used to fabricate the canisters, saving time and money and enabling larger, more complex parts to be mass produced. The project went one step further and creatively proved that these cans could be made from the same material as the final part, thus eliminating post processing. As a final achievement, the project showed that combining HIP/PM with AM created as robust a part as one produced by AM alone, thus offering a cost effective alternative to the more expensive 3DP. EIO's Report is posted on the DOE website www.osti.gov.